The miniaturization of electronics since the early 2000s has sparked a revolution in space technology, driving the rise of small satellites. Over the past decade, significant advancements in related fields—such as launch infrastructure, downlink capacity, inter-satellite communication, and micro-propulsion systems—have made space more accessible and affordable.
Today, companies are building small satellite constellations with tens to hundreds of units, far exceeding the scale of traditional space operations. Imec is at the forefront of this movement, delivering robust, integrated chips for multi- and hyperspectral imaging.
The small satellites monitor, e.g., crop health and yields, the volume of transportation over sea or land, changes in biomass for carbon offset trading, greenhouse gas emissions, implementation of policies (e.g., reforestation), or ecosystem changes, to name but a few of the countless possibilities. They do so in much greater detail, with higher temporal, spatial, and spectral resolution than was previously possible.
Such satellites rely on advanced image sensors to gather the much-needed accurate and detailed data. A differentiating factor of these sensors is their broad spectral range and high signal to noise ratio (SNR). The spectral range allows for the detection of a greater variety of features, while improved SNR ensures that even faint signals can be accurately captured.
As one of the most promising solutions, scientists at imec have developed a wafer-level process to deposit multi- and hyperspectral filters directly on state-of-the-art image sensor chips, resulting in on-chip spectral imaging.
Imec offers a range of ready-made spectral imaging chips, and a versatile design path for those payload- and satellite developers who need a customized, application-specific spectral imaging solution.
From complex instruments to on-chip setups
Spectral imaging for Earth observation has been around for decades, relying on prism and gratings for separating the light into its different color components. The resulting instruments, however, are rather bulky, complex and fragile, and therefore only suitable for large satellite projects.
With the advent of thin-film optical filters coated on glass substrates and fitted in front of imaging chips, it has become possible to build cameras that are lighter, an order of magnitude more compact and with a much simpler system design. That has lifted the barrier to integrating spectral cameras in smaller satellites.
Imec takes optical thin-film filters a step further by coating and patterning them directly onto imager chips, inline in a wafer-based semiconductor process. This on-chip solution offers a number of advantages compared to competing thin-film technologies.
First, depositing filters in a wafer-based semiconductor process results in a controlled, repeatable production of robust spectral imaging chips with very low sensor-to-sensor variability. This makes the sensors ideal for satellite constellations, where consistent data from one satellite to the next are crucial.
Furthermore, the Class 1 cleanroom environment ensures an unparalleled level of cleanliness, which, when combined with the telescopic satellite optics, produces images with an exceptionally low defect count.
The integrated design, where optical material is grown on top of the CMOS sensor’s surface, also guarantees nanometer-precision filter-to-imager alignment and a much higher resilience to shocks, vibrations, and temperature fluctuations—significant advantages in the harsh conditions of space.
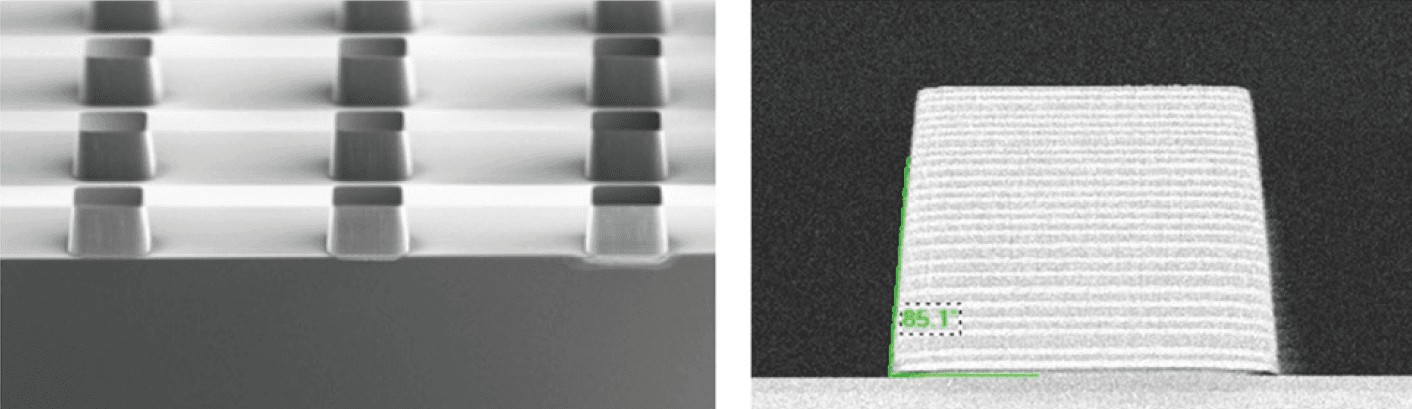
Imec's on-chip solution for spectral imagers is based on Bragg filters. At the left is an SEM of such Bragg filters with a detail of its layers structured at the right. It clearly shows how accurately and uniformly the material layers are deposited on the surface of an image wafer.
Because filter deposition and patterning are done in-process with state-of-the-art semiconductor tools, the precision and reliability are equal to that of the actual image sensor production. This means that filters can be etched in patterns and sizes down to the individual pixels, creating an individual optical filter for each pixel of the imager.
This approach allows for endless flexibility to define highly optimized geometric filter layouts. These include, for example, multi- and hyperspectral line scanners, hybrid line/snapshot scanners, snapshot video imagers or even randomized layouts for compressive or AI sensing.
Linescan sensors are made by patterning a number of filter stripes, each stripe stretching over the full width of the sensor. The stripes can cover one or more pixel lines, resulting in multiple optical filters for mixed mode imaging, multispectral imaging or even hyperspectral imaging (we’ve already patterned a 192-stripes sensor).
The possibility to combine many pixel lines of the detector under one spectral filter band supports digital Time Delayed Integration (TDI) mode, resulting in improved image products with a higher signal-to-noise ratio.
It’s also possible to include filters with different characteristics on the same focal plane, with minimal loss in the transition zones from one filter region to another. Examples are, e.g., mixing of panchromatic zones with multispectral or hyperspectral zones or other types of filters (edge pass, band pass…) This is another way filters can be created that are optimized for their applications.
Imec also developed and demonstrated the capability to integrate the CMOS filters on non-CMOS imaging technologies, such as InGaAs and MCT, opening further access to a fuller spectral range.
Today, our various optical filter designs are already used in space for low-orbit observation and space exploration. Many others are scheduled to be launched soon or are under development in collaboration with our customers to bring their requirements to the best-fitting spectral imaging chip for their instruments.
How to build your Earth observation instrument?
If you are an instrument manufacturer or integrator, or run a small-satellite business, you can choose a sensor from imec’s range of prefabricated hyperspectral and multispectral image sensors, or one of the available cameras for evaluation purposes.
Or you can work with us to develop a custom spectral image sensor. Our design and fabrication process is flexible in terms of optical filters, filter geometry, and imagers used, allowing us to design on-chip spectral imaging solutions that fit your application requirements.
As an example from our portfolio of available spectral imagers, we have recently added a versatile line scanner that captures 96 bands in the 450-900 nanometer spectral range.
The new scanner’s filter is deposited on an AMS CMV2000 image sensor, which has an excellent track record in space applications. The sensor’s 96 bands are equidistantly divided into accurately positioned spectral bands, with a uniform transmission efficiency throughout the complete spectral range. In comparison to its predecessor, we doubled the number of pixel lines on each band, boosting the spectral sensitivity in a digital TDI mode.
Additionally, the sensor can be operated at full spectral resolution or specific bands can be selected for read-out, greatly reducing the data volume and thus increasing the maximum achievable framerate. This allows application designers to choose the optimal mix of frame rate, data throughput, and signal-to-noise ratio.
In addition to the line scanners we already offer, imec’s flexible process allows to create line scanners with stepped filters in any configuration. There’s flexibility to define the number of steps, enabling, e.g., hyperspectral scanning in 150+ bands as well as to choose the width of the steps, i.e., the number of pixel lines for each step, which helps boost the signal-to-noise ratio. The filtered bands can be equidistantly divided or not, and the spectrum scanned can be visible, near-infrared, or short-wave infrared.
Innovative filter layouts for more options
Line scanners generate a large amount of data. Each point in the scene needs to be observed across multiple frames before its spectral signature can be fully reconstructed. All that data then has to be either preprocessed and compressed in the satellite or sent as raw data to a ground station, requiring much energy and a broad data link.
However, not all applications require continuous scanning at the highest data rate.
To improve the data efficiency of Earth observation, we have created filter designs that combine line scanning with snapshot imaging. Snapshot imaging is normally done with a mosaic filter layout where, e.g., 4x4 or 5x5 imager pixels are overlaid with a spectral filter of 16 or 25 bands, respectively. Such a mosaic layout captures a spectral cube dataset in each frame, albeit in less detail.
The new hybrid layout—line scanner and snapshot scanner in one—can be operated in a low-data-rate, low-resolution mode for early detection and a high-resolution, high-data-rate mode for more accurate scanning, switching between modes during flight by modifying the camera frame rate. Use cases include early detection of fires or other temporary events, or capturing more detailed images of the same scene for temporal analysis.
Other layouts include combining a number of discrete lines and a mosaic on one imager. This allows for a very sensitive scan in a few specific bands combined with less sensitive detection for other bands.
Lastly, we’re also working with multi-resolution mosaic layouts and randomized layouts for compressive sensing.
Your one-stop shop for spectral Earth observation
As a technology partner of some of the world’s most demanding electronics companies, we have a proven track record of moving technology to a high readiness level. Our engineers ensure the best fit between application needs and technology requirements, creating excellent off-the-shelf products and flexible processes that allow for highly customized designs.
To tackle our planet’s many challenges, we need data on both local and global scales. Sensor data that we can now collect thanks to the ability to launch powerful but relatively cheap small satellites. Imec’s innovative spectral imaging technology is here to help drive this evolution. With our portfolio of available sensors and the flexibility to design custom imagers in a development-on-demand project, imec is a one-stop shop for camera builders and payload integrators seeking high-precision, high-quality sensors for Earth observation from small satellites.
Together, we will build a new generation of instruments to monitor our living planet and signal where action should be taken to preserve it in good health for our generation and the next.
Contact us today, to discuss and see how we may help with your project
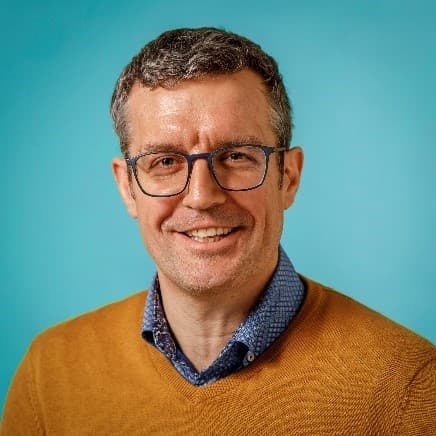
Bavo Delauré is the project leader for space related developments at imec in the domain of on-chip spectral imaging. He received a Ph.D. in Physics in 2004 from the KULeuven. He has 16 years of experience in the development of compact multi-and hyperspectral payloads for earth observation from UAV’s and small satellites at VITO Remote Sensing (B). In 2021 he joined imec and currently he is driving the space projects at imec related to on-chip spectral imaging. The unique technique developed at imec to deposit optical filters at wafer level allows to create imaging chips sensitive from VNIR until SWIR with spatially patterned optical filters in various forms including but not limited to line-based or mosaic like geometries.
Published on:
12 November 2024